13/11/2019
Proposta de Plano de Manutenção Industrial Para Uma Empresa do Setor Moveleiro
Elisandro Grenzel Eduardo Luis Volken
PROPOSTA DE PLANO DE MANUTENÇÃO INDUSTRIAL PARA UMA EMPRESA DO SETOR MOVELEIRO
Horizontina – RS 2017
PROPOSTA DE PLANO DE MANUTENÇÃO INDUSTRIAL PARA UMA EMPRESA DO SETOR MOVELEIRO
Horizontina – RS 2017
Elisandro Grenzel Eduardo Luis Volken
PROPOSTA DE PLANO DE MANUTENÇÃO INDUSTRIAL PARA UMA EMPRESA DO SETOR MOVELEIRO
Trabalho Final para aprovação da Disciplina de Manutenção Industrial, do Curso de Engenharia de Produção, sob a orientação do Prof. Esp. Jackson Luis Bartz.
Horizontina – RS 2017
RESUMO
Este estudo de caso trabalhou no planejamento de um plano de manutenção possível frente à realidade apresentada em uma indústria moveleira, localizada no Noroeste do Rio Grande do Sul, avaliando a dinâmica de funcionamento da empresa e focando em um projeto de prevenção de danos e agravos. Para realização do mesmo, foram realizados visitas de caráter observatório nas dependências da indústria onde se conheceu a rotina de funcionamento e os serviço, caracterizando as máquinas utilizadas incluindo o levantamento de falhas crônicas dos equipamentos, as causas das falhas, a verificação de melhorias já realizadas nos equipamentos e a elaboração de um plano de manutenção. Com o objetivo de mostrar os ganhos com a implantação da manutenção preventiva dos equipamentos estando aptos ao uso e diminuir gastos com interrupções dos serviços por quebra ou funcionamento inadequado do mesmo, confirmar a importância de um sistema de gestão da manutenção, identificar as principais ações estratégicas que poderiam contribuir para melhorar a produtividade e reduzir os custos de manutenções. Conclui-se que a manutenção é peça chave para garantir o bom funcionamento de um processo produtivo, sendo assim de grande valia a boa gestão de um plano de manutenção apropriado, conforme o que o empresa prioriza como importante.
Palavras chave: Equipamento, Manutenção, Indústria Moveleira, Proteção.
ABSTRACT
This case study worked on the planning of a possible maintenance plan facing the reality presented in a furniture manufacturer industry, located in the Northwest of Rio Grande do Sul, evaluating the dynamics of the company's operation and focusing on a project to prevent damages and Injuries Observatory visits were carried out at the premises of the industry where the routine of operation and service of the same was observed, characterizing the used machines included the survey of chronic equipment failures, causes of failures, verification of improvement in the Equipment and the preparation of a maintenance plan for the equipment evaluated. With the objective of showing the gains with the implementation of preventive maintenance of the equipment, being able to use and reduce expenses with interruptions of the services due to breakage or inadequate operation of the same, to confirm the importance of a maintenance management system, to identify the main actions Which could contribute to improving productivity and reducing maintenance costs. We concluded that
Key words: Equipment, Maintenance, Furniture industry, Protection.
LISTA DE FIGURAS
FIGURE 1 - MODELO ESTRATÉGIAS MISTAS ..................................................................................................................... 15 FIGURE 2 - MODELO CENÁRIOS ESTRATÉGICOS MISTOS ..................................................................................................... 16 FIGURE 3 - MODELO MATRIZ ESTRATÉGICA ..................................................................................................................... 17 FIGURE 4 - CHECKLIST FRESA ........................................................................................................................................ 22 FIGURE 5 - CHECKLIST COLADEIRA ................................................................................................................................. 23 FIGURE 6 - CHECKLIST FURADEIRA ................................................................................................................................. 24 FIGURE 7 - CHECKLIST RESPIGADEIRA ............................................................................................................................. 24 FIGURE 8 - CHECKLIST ENVERNIZADORA .......................................................................................................................... 25 FIGURE 9 - CHECKLIST LIXADEIRA ................................................................................................................................... 25 FIGURE 10 - CHECKLIST TRANSFER ................................................................................................................................. 26 FIGURE 11 - CHECKLIST TÚNEL DE SECAGEM .................................................................................................................... 26 FIGURE 12 - CHECKLIST MENSAL .................................................................................................................................... 27 FIGURE 13 - CONTROLE FINANCEIRO DE MANUTENÇÃO ..................................................................................................... 27
SUMÁRIO
1 INTRODUÇÃO .......................................................................................................................................... 7 1.1 TEMA ...................................................................................................................................................... 7 1.2 PROBLEMA DE PESQUISA ....................................................................................................................... 8 1.3 OBJETIVOS .............................................................................................................................................. 8 1.3.1 Objetivo Geral .................................................................................................................................... 8 1.3.2 Objetivos Específicos .......................................................................................................................... 8 1.4 JUSTIFICATIVA ........................................................................................................................................ 8 2 REVISÃO DE LITERATURA ......................................................................................................................... 9 2.1 MANUTENÇÃO INDUSTRIAL ................................................................................................................... 9 2.2 HISTÓRICO DA MANUTENÇÃO ............................................................................................................... 9 2.2.1 A Primeira Geração ............................................................................................................................ 9 2.2.2 A Segunda Geração ........................................................................................................................... 9 2.2.3 A Terceira Geração ............................................................................................................................ 9 2.3 TIPOS DE MANUTENÇÃO ...................................................................................................................... 11 2.3.1 Manutenção Corretiva ..................................................................................................................... 11 2.3.2 Manutenção Preventiva .................................................................................................................. 12 2.3.3 Manutenção Preditiva ..................................................................................................................... 13 2.3.4 Manutenção Detectiva .................................................................................................................... 13 2.3.5 Engenharia de Manutenção ............................................................................................................ 14 2.4 MANUTENÇÃO ESTRATÉGICA .............................................................................................................. 14 2.4.1 Terceirização .................................................................................................................................... 14 2.4.2 Meta-estratégias ............................................................................................................................. 15 2.4.3 Estratégias Mistas ........................................................................................................................... 15 2.4.4 Cenários Estratégicos Mistos ........................................................................................................... 16 2.4.5 Matriz Estratégica ........................................................................................................................... 16 2.4.6 Estratégia da Produção ................................................................................................................... 17 2.5 SISTEMAS DE INFORMAÇÃO................................................................................................................. 17 3 METODOLOGIA .......................................................................................................................................19 3.1 APRESENTAÇÃO DA EMPRESA ............................................................................................................. 19 3.2 DELIMITAÇÃO DO PROCESSO DE MANUTENÇÃO EXISTENTE ............................................................... 20 4 APRESENTAÇÃO E ANÁLISES DOS RESULTADOS ......................................................................................21 4.1 PROPOSTA DE PLANO DE MANUTENÇÃO DAS MÁQUINAS .................................................................. 21 4.1.1 Fresadora ......................................................................................................................................... 21 4.1.2 Coladeira .......................................................................................................................................... 22 4.1.3 Furadeira ......................................................................................................................................... 23 4.1.4 Respigadeira .................................................................................................................................... 24 4.1.5 Envernizadora .................................................................................................................................. 24 4.1.6 Lixadeira .......................................................................................................................................... 25 4.1.7 Transfer ............................................................................................................................................ 25 4.1.8 Túnel ................................................................................................................................................ 26 4.2 CONTROLE DA MANUTENÇÃO DAS MÁQUINAS ................................................................................... 26 4.3 CONTROLE FINANCEIRO DA MANUTENÇÃO ........................................................................................ 27
5 CONCLUSÃO ...........................................................................................................................................28
6 REFERÊNCIAS ..........................................................................................................................................29
1 INTRODUÇÃO
O setor moveleiro brasileiro vem crescendo nos últimos anos, alavancando empresas de pequeno porte neste segmento. Segundo a Movergs (2016), o Rio Grande do Sul possui 2.750 empresas moveleiras, o que equivale a 13,3% das empresas do Brasil. Elas respondem por 18,4% do total de móveis fabricados no país e por 31,1% das exportações. Ainda citando a Movergs (2016), em 2015, as indústrias de móveis gaúchas foram responsáveis pela geração de mais de 35 mil postos de emprego. Esses indicadores demonstram que esse segmento é representativo no contexto da economia gaúcha, tanto pela geração de renda e tributos, quanto para números de postos de trabalho. Atualmente se fala muito em aumentar a produtividade e diminuir custos nas empresas, devido à grande concorrência do mercado. Em decorrência disto as empresas vêm procurando agregar qualidade como um diferencial, e assim estar a alturas das exigências padrões. Partindo deste ponto a indústria começou a investir em equipamentos que fossem capazes de produzir de forma mais eficiente e com maior qualidade, substituindo parte da mão de obra por tecnologias e princípios de logística. Entretanto, como em toda mudança, surgiram questões operacionais referentes à necessidade de manutenção e o alto custo deste processo para manter estes equipamentos em estado viável de uso. Muitas indústrias até hoje veem neste fato um grande problema. Destaca-se aqui que a manutenção é de extrema importância para o funcionamento da empresa, pois não adianta o administrador melhorar a produção (produtividade) da empresa, se as máquinas e equipamentos não operam de acordo com a necessidade da empresa. O plano de manutenção tem por objetivo antecipar os problemas, permitindo uma redução nos tempos de parada das máquinas, quando for necessário fazer uma manutenção. Podemos constatar então, que existe uma tendência de incorporar nas indústrias a área de manutenção de forma estratégica para resultados promissores nos negócios, pois por meio da manutenção constante e sistemática é possível prever e evitar defeitos. Da mesma forma, é possível detectar uma rotina onde haja expectativa de parada não programada ou padrão não adequado e programar-se para uma intervenção em momento planejado e desejável, sem interromper com os contratos de fornecedores e clientes conferindo confiabilidade a indústria. Perante ao exposto este trabalho tem como objetivo analisar a atual situação da manutenção na empresa e posteriormente propor um plano de manutenção. A empresa é de pequeno porte, atua no ramo moveleiro e está localizada em Três de Maio - RS.
1.1 TEMA
O presente trabalho é um estudo da aplicação da manutenção em uma empresa no setor moveleiro. Através da análise dos procedimentos atuais e proposição de soluções, com base nas melhores práticas e nas possíveis condições.
1.2 PROBLEMA DE PESQUISA
O problema da pesquisa é: Definir e analisar as máquinas em que será aplicado o plano de manutenção, e após responder a seguinte pergunta: Qual é o melhor tipo de manutenção a ser aplicado na empresa?
1.3 OBJETIVOS
1.3.1 Objetivo Geral
O Objetivo geral, do presente estudo será a elaboração de um plano atualizado de manutenção de equipamentos de uma indústria do setor moveleiro. Com os objetivos específicos de realizar um levantamento dos atuais equipamentos e do tipo de manutenção implantado, propondo conceitos inovadores que possam contribuir para aumentar os padrões de competitividade da indústria pesquisada no mercado.
1.3.2 Objetivos Específicos
Os objetivos específicos do estudo são: Fundamentar conceitualmente manutenção, tipos de manutenção e plano de manutenção; Identificar os problemas de manutenção na empresa estudada; Propor melhorias para a manutenção das máquinas da empresa; Então utilizando as técnicas e elaborando os procedimentos acima citados, será trabalhado na elaboração do plano de manutenção afim de atingir os objetivos proposto.
1.4 JUSTIFICATIVA
Atualmente não existe, um planejamento das manutenções da empresa, tendo este fato acarretado em um número alto de paradas de produção por falhas em equipamentos. Com um planejamento adequado, a empresa diminuirá as sequências de falhas nos equipamentos e, por consequência, um custo de produção mais baixo, gerando mais lucros, sendo este o principal objetivo de qualquer empresa. Este estudo se justifica pela necessidade de adquirir conhecimentos referentes aos vários tipos de planos de manutenção de equipamentos para adquirir subsídios para intervir e propor um plano atualizado de manutenção para uma indústria moveleira da região noroeste do estado do Rio Grande do Sul. Pois a grande maioria das indústrias da região realizam concertos da forma corretiva não planejada, ou seja, quando ocorre a falha ou quebra é efetuado o reparo, que gera maiores custos e prejuízos para a empresa. Para isso, se faz necessário uma análise da estrutura e das operações realizadas pela indústria objeto deste estudo para elaborar uma proposta de plano de manutenção industrial neste setor, demonstrando ao empresário a possibilidade de ganho com o investimento inicial em prevenção de interrupções não esperada dos serviços.
2 REVISÃO DE LITERATURA
2.1 MANUTENÇÃO INDUSTRIAL
A manutenção industrial é um conjunto de ações necessárias para manter ou restaurar uma peça, equipamento, máquina ou sistema com o objetivo fazer com que o equipamento continue operando e atingindo sua a máxima vida útil. Para que as empresas se mantenham competitivas e com e excelência operacional, a manutenção deve assumir cada vez mais uma função estratégica nas organizações. Como ela é a responsável pela disponibilidade dos ativos, acaba tendo uma importância capital nos resultados da empresa sendo eles tão melhores quanto mais eficaz for a gestão da manutenção industrial (SILVEIRA, 2016).
2.2 HISTÓRICO DA MANUTENÇÃO
Segundo Moubray (1997) a história da manutenção, em aspecto geral, pode ser dividida em três momentos distintos:
2.2.1 A Primeira Geração
Ocorreu no período que antecedeu a Segunda Guerra Mundial. Os produtos eram confeccionados de forma artesanal, a produção era pequena assim como a organização do processo produtivo. Os equipamentos exigiam projetos mínimos e sua manutenção era de fácil execução dependendo basicamente de limpeza e lubrificação aleatória (MOUBRAY, 1997).
2.2.2 A Segunda Geração
Esta geração é caracterizada como período pós-guerra, e que foi até os anos 60, nessa época houve aumento da demanda por diversos tipos de produtos e em grandes quantidades, o que exigiu equipamentos maiores e mais complexos. Com este vislumbro de tecnologia surgem os planos de manutenção de equipamentos, que passam a ser elaborados pelas indústrias. Além disso, entra em cena a preocupação com as interrupções inesperadas na produção e passa-se a considerar que falhas nos equipamentos poderiam e deveriam ser previstas. Em contrapartida, aumentam assim os custos e o controle do processo de manutenção (MOUBRAY, 1997).
2.2.3 A Terceira Geração
Esta geração teve início a partir da década de 70. Foi um momento em que a indústria buscou novas maneiras de maximizar a vida útil dos equipamentos produtivos, preocupando-se com disponibilidade e confiabilidade, aparece à produção em larga escala, a organização do trabalho, a automatização da produção, conceitos de preservação ambiental, segurança e qualidade dos produtos e viabilidade dos custos operacionais (MOUBRAY, 1997). Segundo Simeón (2008), nesta geração da manutenção, que a Engenharia de Manutenção assume posição mais destacada como um departamento. Após este breve histórico sobre a evolução da manutenção, podemos
2.1 MANUTENÇÃO INDUSTRIAL
A manutenção industrial é um conjunto de ações necessárias para manter ou restaurar uma peça, equipamento, máquina ou sistema com o objetivo fazer com que o equipamento continue operando e atingindo sua a máxima vida útil. Para que as empresas se mantenham competitivas e com e excelência operacional, a manutenção deve assumir cada vez mais uma função estratégica nas organizações. Como ela é a responsável pela disponibilidade dos ativos, acaba tendo uma importância capital nos resultados da empresa sendo eles tão melhores quanto mais eficaz for a gestão da manutenção industrial (SILVEIRA, 2016).
2.2 HISTÓRICO DA MANUTENÇÃO
Segundo Moubray (1997) a história da manutenção, em aspecto geral, pode ser dividida em três momentos distintos:
2.2.1 A Primeira Geração
Ocorreu no período que antecedeu a Segunda Guerra Mundial. Os produtos eram confeccionados de forma artesanal, a produção era pequena assim como a organização do processo produtivo. Os equipamentos exigiam projetos mínimos e sua manutenção era de fácil execução dependendo basicamente de limpeza e lubrificação aleatória (MOUBRAY, 1997).
2.2.2 A Segunda Geração
Esta geração é caracterizada como período pós-guerra, e que foi até os anos 60, nessa época houve aumento da demanda por diversos tipos de produtos e em grandes quantidades, o que exigiu equipamentos maiores e mais complexos. Com este vislumbro de tecnologia surgem os planos de manutenção de equipamentos, que passam a ser elaborados pelas indústrias. Além disso, entra em cena a preocupação com as interrupções inesperadas na produção e passa-se a considerar que falhas nos equipamentos poderiam e deveriam ser previstas. Em contrapartida, aumentam assim os custos e o controle do processo de manutenção (MOUBRAY, 1997).
2.2.3 A Terceira Geração
Esta geração teve início a partir da década de 70. Foi um momento em que a indústria buscou novas maneiras de maximizar a vida útil dos equipamentos produtivos, preocupando-se com disponibilidade e confiabilidade, aparece à produção em larga escala, a organização do trabalho, a automatização da produção, conceitos de preservação ambiental, segurança e qualidade dos produtos e viabilidade dos custos operacionais (MOUBRAY, 1997). Segundo Simeón (2008), nesta geração da manutenção, que a Engenharia de Manutenção assume posição mais destacada como um departamento. Após este breve histórico sobre a evolução da manutenção, podemos
perceber a mudança do conceito da atividade de manutenção de equipamentos, que iniciou com foco em restabelecer com maior praticidade possível as condições dos equipamentos e evoluiu para se se preocupar em prevenir a ocorrência das falhas. A manutenção segundo a Associação Brasileira de Normas Técnicas (NBR 5462, 1994) é definida como a "combinação de todas as ações técnicas e administrativas, incluindo as de supervisão, destinadas a manter ou recolocar um item em estado no qual possa desempenhar uma função requerida". Já Viana (2008) reforça esta definição quando afirma que a manutenção é uma palavra derivada do latim manus tenere, que significa manter o que se tem e acompanha a humanidade ao decorrer do tempo, desde quando o homem inicia o manuseio de instrumentos de produção. Como manutenção preventiva a ABNT (1994) afirma como definição da mesma, a manutenção realizada com intervalos predeterminados, ou seguindo critérios prescritos, que se destinam a atenuar e reduzir a probabilidade de defeitos ou a degradação. Souza (2009) diz que toda manutenção preventiva tem o dever de ser pensada e prevista. Por conseguinte, ocorrerá a inexistência de situações não esperadas. O imprevisto será apenas uma ação corretiva e que deverá ser denominada como tal, percebendo onde se encontram os problemas de base, suas potenciais causas e as ações que devem ser desencadeadas para corrigir o erro. Filho (2005) em seus trabalhos traz o conceito de gerência da manutenção, que representa um conjunto de atos, normas e instruções de procedimentos pertencentes a um sistema de manutenção, que direciona os trabalhos e a função de um departamento de manutenção. Sendo que a finalidade da gerência da manutenção é a de estruturar metas e objetivos através de normas de trabalho para que se alcancem um melhor uso de pessoal, máquinas e materiais em uma indústria. Zaions (2003) afirma algumas vantagens na manutenção preventiva, segundo ele algumas delas são a continuidade do funcionamento do equipamento, que apenas irá pausar seu funcionamento para consertos em horas programadas; promovendo a produção continuada, devido à confiabilidade funcional do equipamento, sendo viável para a indústria planejar metas de produção fechando contratos com prazos de entrega otimizados e na qualidade exigida pelo mercado globalizado. A manutenção preventiva vai contra o que preza a manutenção corretiva, muito usada por indústrias, que segundo Monchy (1989), consiste em manter o equipamento em funcionamento, até que ocorra a inevitável degradação do mesmo. Sendo assim, ocorre apenas à troca de peças danificadas, quando o equipamento sofre parada abrupta ou apresenta defeito no material final produzido. O autor afirma ainda que manutenção realizada apenas de forma corretiva é o mesmo que “submeter-se, sofrer”. Mencionamos também, Mirshawka (1993) que conceitua manutenção como um apanhado de ações e recursos dispensados em um equipamento, com objetivo de manter sua capacidade funcional dentro da necessidade de sua disponibilidade, para cumprir os prazos sem deixar de considerar a qualidade e os custos dentre outros. Manutenção é um processo que visa maior tempo de utilização e maior rendimento de um equipamento, resultando em trabalho com condições seguras e redução de custos com paradas. A estes cuidados estão envolvidos a adequação, a restauração, a substituição, a conservação e a prevenção. Portanto, sua principal atribuição é garantir a disponibilidade da função dos equipamentos e instalações de modo que venha há atender um processo de produção e a preservação do meio ambiente, com confiabilidade, segurança e custo adequados. (FLORES, 2015) Sabemos que os equipamentos, independentemente de quais sejam, necessitam de manutenções, que estabeleçam sua operabilidade e funcionalidade seguindo requisitos legais de segurança, seja ela do trabalhador, do consumidor ou ambiental. Podendo ser executada nas indústrias através de duas abordagens: atividades proativas, que são realizadas antes do defeito ocorrer e atividades reativas que atuam quando o equipamento falha (MOUBRAY, 1997).
2.3 TIPOS DE MANUTENÇÃO
Segundo Pinto (2001, pg. 35), a maneira pela qual é feita a intervenção nos equipamentos, sistemas ou instalações caracteriza os vários tipos de manutenção existentes, citadas a seguir.
2.3.1 Manutenção Corretiva
Ao atuar em um equipamento que apresenta um defeito ou um desempenho diferente do esperado estamos fazendo manutenção corretiva. Assim, ela não é necessariamente uma manutenção de emergência. Em outras palavras, a manutenção corretiva é a atuação para a correção da falha ou do desempenho menor que o esperado (PINTO 2001, pg. 36). A manutenção corretiva é dividida em duas: Manutenção Corretiva Não Planejada e Manutenção Corretiva Planejada (PINTO 2001, pg. 36).
2.3.1.1 Manutenção Corretiva Não Planejada Manutenção corretiva não planejada é a correção da falha de maneira aleatória. Desta forma, caracteriza-se pela atuação da manutenção em fato já ocorrido, seja este uma falha ou um desempenho menor que o esperado. Não há tempo para preparação do serviço. Infelizmente ainda é mais praticado do que deveria (PINTO 2001, pg. 37). Normalmente ela implica em altos custo, pois a quebra inesperada pode acarretar perdas de produção, perda da qualidade do produto e elevados custos indiretos de manutenção (PINTO 2001, pg. 37). Além disso, os equipamentos também podem ter seus defeitos e falhas aleatórios potencializados, ou seja, os prejuízos podem ser maiores, e uma troca de uma simples peça pode representar a perda total de uma máquina. (PINTO, 2001). Sem contar, que em indústrias com elevados riscos físicos e químicos de produção. Que atuam com altas temperaturas e pressões, produtos tóxicos e inflamáveis um equipamento com defeito pode causar uma catástrofe de repercussão em massa. Quando se interrompe o trabalho de um equipamento, gera-se o efeito dominó ou cascata, ou seja, compromete o desempenho de outros equipamentos que vinham operando em condições regulares, levando-os a parar os trabalhos ou a redução da produção. Portanto, se a indústria tiver a sua manutenção de equipamento da forma corretiva no subtipo não planejado, o departamento de manutenção acaba sendo norteado pelos equipamentos e o desempenho da indústria não suprirá as demandas e cobranças do mercado globalizado.
Segundo Pinto (2001, pg. 35), a maneira pela qual é feita a intervenção nos equipamentos, sistemas ou instalações caracteriza os vários tipos de manutenção existentes, citadas a seguir.
2.3.1 Manutenção Corretiva
Ao atuar em um equipamento que apresenta um defeito ou um desempenho diferente do esperado estamos fazendo manutenção corretiva. Assim, ela não é necessariamente uma manutenção de emergência. Em outras palavras, a manutenção corretiva é a atuação para a correção da falha ou do desempenho menor que o esperado (PINTO 2001, pg. 36). A manutenção corretiva é dividida em duas: Manutenção Corretiva Não Planejada e Manutenção Corretiva Planejada (PINTO 2001, pg. 36).
2.3.1.1 Manutenção Corretiva Não Planejada Manutenção corretiva não planejada é a correção da falha de maneira aleatória. Desta forma, caracteriza-se pela atuação da manutenção em fato já ocorrido, seja este uma falha ou um desempenho menor que o esperado. Não há tempo para preparação do serviço. Infelizmente ainda é mais praticado do que deveria (PINTO 2001, pg. 37). Normalmente ela implica em altos custo, pois a quebra inesperada pode acarretar perdas de produção, perda da qualidade do produto e elevados custos indiretos de manutenção (PINTO 2001, pg. 37). Além disso, os equipamentos também podem ter seus defeitos e falhas aleatórios potencializados, ou seja, os prejuízos podem ser maiores, e uma troca de uma simples peça pode representar a perda total de uma máquina. (PINTO, 2001). Sem contar, que em indústrias com elevados riscos físicos e químicos de produção. Que atuam com altas temperaturas e pressões, produtos tóxicos e inflamáveis um equipamento com defeito pode causar uma catástrofe de repercussão em massa. Quando se interrompe o trabalho de um equipamento, gera-se o efeito dominó ou cascata, ou seja, compromete o desempenho de outros equipamentos que vinham operando em condições regulares, levando-os a parar os trabalhos ou a redução da produção. Portanto, se a indústria tiver a sua manutenção de equipamento da forma corretiva no subtipo não planejado, o departamento de manutenção acaba sendo norteado pelos equipamentos e o desempenho da indústria não suprirá as demandas e cobranças do mercado globalizado.
2.3.1.2 Manutenção Corretiva Planejada A manutenção corretiva planejada é a correção do desempenho menor que o esperado ou da falha, por decisão gerencial, isto é, pela atuação em função de acompanhamento preditivo ou pela decisão de operar até a quebra. Mesmo que a decisão foi de deixar a máquina funcionar até quebrar essa é uma decisão conhecida e algum planejamento pode ser feito quando a falha ocorrer (PINTO 2001, pg. 38). É a correção do equipamento que está com limitações em seu funcionamento, por decisão do empresário, isto é, realizam um acompanhamento preditivo e decidem agir em momentos qualquer ou operar até a quebra. (PINTO e XAVIER, 2007, p. 34). A manutenção realizada deste modo dependerá do acompanhamento feito e da informação obtidas para planejamento da execução das tarefas. Neste tipo de manutenção, de certa forma, os gastos podem ser menores já que se opera esperando a falha ou a perda de rendimento do equipamento.
2.3.2 Manutenção Preventiva
A manutenção preventiva é a atuação realizada de forma a reduzir ou evitar a falha ou queda no desempenho, obedecendo a um plano previamente elaborado, baseado em intervalos definidos de tempo (PINTO 2001, pg. 38). Desta forma, ao contrário da manutenção corretiva, a preventiva busca evitar a ocorrência da falha, ou seja, prevenir. Em casos que representam a segurança, como na aviação, a manutenção preventiva é indispensável (PINTO 2001, pg. 38). Segundo Pinto & Nassif, 2001 a manutenção Preventiva é a atuação realizada de forma a reduzir ou evitar a falha ou queda no desempenho, obedecendo a um plano previamente elaborado, baseado em intervalos definidos de tempo. Pereira (2009) diz que a necessidade de realizar alguma manutenção preventiva teve início em 1930, na indústria aeronáutica ou de aviação, pois as aeronaves deveriam estarem e se manter disponíveis para uso garantindo principalmente a confiabilidade e a segurança dos voos. Outro ponto relevante em um mercado acirrado e de grande concorrência, independentemente do polo produtivo, é manter-se com o negócio em pleno funcionamento, ativo, e com diferenciais que aumentem o cartel de serviços, sendo um potencial competitivo e atualizado frente às necessidades imediatistas da sociedade de consumo. Segundo alguns autores a manutenção Preventiva também pode apresentar alguns defeitos, como na citação abaixo: A manutenção preventiva tem um lado negativo, pois pode introduzir defeitos não existentes no equipamento devido a: falhas humanas, falhas nos componentes sobressalentes, contaminações em sistemas de óleo dos equipamentos, falhas ocasionadas durante partidas e paradas dos equipamentos, e falhas nos procedimentos de manutenção. (NOGUEIRA, GUIMARÃES, SILVA, 2012) Como potenciais qualidades têm autores que trazem: Entretanto, se por um lado a manutenção preventiva proporciona conhecimento prévio das ações, permitindo uma boa condição de gerenciamento das atividades e nivelamento de recursos, além de previsibilidade de consumo de materiais e sobressalentes, por outro, promove, via de regra, a retirada do equipamento ou sistemas de operação para execução dos serviços programados. Desta forma, possíveis questionamentos à política de manutenção preventiva sempre serão levantados em equipamentos, sistemas ou plantas onde o conjunto de fatores não seja suficiente forte ou claro em prol dessa política. (PINTO, 2001).
2.3.2 Manutenção Preventiva
A manutenção preventiva é a atuação realizada de forma a reduzir ou evitar a falha ou queda no desempenho, obedecendo a um plano previamente elaborado, baseado em intervalos definidos de tempo (PINTO 2001, pg. 38). Desta forma, ao contrário da manutenção corretiva, a preventiva busca evitar a ocorrência da falha, ou seja, prevenir. Em casos que representam a segurança, como na aviação, a manutenção preventiva é indispensável (PINTO 2001, pg. 38). Segundo Pinto & Nassif, 2001 a manutenção Preventiva é a atuação realizada de forma a reduzir ou evitar a falha ou queda no desempenho, obedecendo a um plano previamente elaborado, baseado em intervalos definidos de tempo. Pereira (2009) diz que a necessidade de realizar alguma manutenção preventiva teve início em 1930, na indústria aeronáutica ou de aviação, pois as aeronaves deveriam estarem e se manter disponíveis para uso garantindo principalmente a confiabilidade e a segurança dos voos. Outro ponto relevante em um mercado acirrado e de grande concorrência, independentemente do polo produtivo, é manter-se com o negócio em pleno funcionamento, ativo, e com diferenciais que aumentem o cartel de serviços, sendo um potencial competitivo e atualizado frente às necessidades imediatistas da sociedade de consumo. Segundo alguns autores a manutenção Preventiva também pode apresentar alguns defeitos, como na citação abaixo: A manutenção preventiva tem um lado negativo, pois pode introduzir defeitos não existentes no equipamento devido a: falhas humanas, falhas nos componentes sobressalentes, contaminações em sistemas de óleo dos equipamentos, falhas ocasionadas durante partidas e paradas dos equipamentos, e falhas nos procedimentos de manutenção. (NOGUEIRA, GUIMARÃES, SILVA, 2012) Como potenciais qualidades têm autores que trazem: Entretanto, se por um lado a manutenção preventiva proporciona conhecimento prévio das ações, permitindo uma boa condição de gerenciamento das atividades e nivelamento de recursos, além de previsibilidade de consumo de materiais e sobressalentes, por outro, promove, via de regra, a retirada do equipamento ou sistemas de operação para execução dos serviços programados. Desta forma, possíveis questionamentos à política de manutenção preventiva sempre serão levantados em equipamentos, sistemas ou plantas onde o conjunto de fatores não seja suficiente forte ou claro em prol dessa política. (PINTO, 2001).
2.3.3 Manutenção Preditiva
Também conhecida como Manutenção Sob Condição ou Manutenção com Base no Estado do Equipamento é a atuação realizada com base em modificação de parâmetro de condição ou desempenho, cujo acompanhamento obedece a uma sistemática (PINTO 2001, pg. 41). A manutenção preditiva não promove a intervenção nos equipamentos ou sistemas, pois as medições e verificações são efetuadas com o equipamento produzindo. Quando o grau de degradação se aproxima ou atinge o limite previamente estabelecido, é tomada a decisão de intervenção (PINTO 2001, pg. 42). A manutenção preditiva não deixa de ser uma manutenção preventiva baseada nas condições dos equipamentos. Neste plano, ocorre o acompanhamento do equipamento através de medições adotadas e feitas quando o mesmo estiver em pleno funcionamento, o que facilita uma maior disponibilidade, já que o equipamento vai sofrer intervenção, apenas no limiar estabelecido antecipadamente pelo departamento de manutenção. Entende-se com isso, que a manutenção preditiva antecipa a falha do equipamento e quando se decide realizar a intervenção para o conserto, ocorre na verdade uma manutenção corretiva programada. As condições básicas para que seja estabelecido este tipo de manutenção, são as seguintes: o equipamento, sistema ou instalação deve permitir algum tipo de monitoramento. O equipamento, sistema ou instalação deve ter a escolha por este tipo de manutenção justificada pelos custos envolvidos. As falhas devem ser originadas de causas que possam ser monitoradas e ter sua progressão acompanhada. (NOGUEIRA, GUIMARÃES, SILVA, 2012) Ou seja, podemos dizer que a manutenção preditiva, é empenho realizado para acompanhar e monitorar as condições apresentadas pelo equipamento. A mesma está condicionada a detecção precoce dos sintomas da falha. O que demanda ter instrumentos de medição adequados, bom programa de computador e treinamento de pessoal é que faz com que a manutenção preditiva seja uma das mais baratas e seguras para conduzir uma política de manutenção.
2.3.4 Manutenção Detectiva
A manutenção detectiva é a atuação efetuada em sistemas de proteção, buscando detectar falhas ocultas ou não perceptíveis ao pessoal de operação e manutenção (PINTO 2001, pg. 44). A identificação de falhas ocultas é primordial para gerar confiabilidade. Em sistemas complexos essas ações devem ser efetuadas por pessoal da área de manutenção, com treinamento e habilitação para tal, assessorado pelos operadores das máquinas. Atualmente torna se necessário o uso de máquinas com controle autônomo e a crescente a utilização de computadores para o controle de processo nos mais diversos tipos de plantas fabris (PINTO 2001, pg. 44). A manutenção detectiva começou a ser mencionada na literatura a partir da década de 90. Sua denominação Detectiva está ligada à palavra Detectar, traduzida do inglês traduz Detective Maintenance. (KARDEC; NASCIF, 2002). Desse modo, Kardec e Nascif (2002), definem a manutenção detectiva como a atuação efetuada em sistemas de proteção, buscando detectar falhas ocultas ou não perceptíveis ao pessoal de operação e manutenção. Conforme Kardec e Nascif (2002), a identificação de falhas ocultas é primordial para garantir a confiabilidade. Em sistemas complexos essas ações só devem ser levadas a efeito por pessoal da área de manutenção, com treinamento e habilitação para tal, assessorado pelo pessoal da operação. Atualmente, é crescente a utilização de computadores para instrumentação e controle de processo nos mais diversos tipos de plantas industriais.
Também conhecida como Manutenção Sob Condição ou Manutenção com Base no Estado do Equipamento é a atuação realizada com base em modificação de parâmetro de condição ou desempenho, cujo acompanhamento obedece a uma sistemática (PINTO 2001, pg. 41). A manutenção preditiva não promove a intervenção nos equipamentos ou sistemas, pois as medições e verificações são efetuadas com o equipamento produzindo. Quando o grau de degradação se aproxima ou atinge o limite previamente estabelecido, é tomada a decisão de intervenção (PINTO 2001, pg. 42). A manutenção preditiva não deixa de ser uma manutenção preventiva baseada nas condições dos equipamentos. Neste plano, ocorre o acompanhamento do equipamento através de medições adotadas e feitas quando o mesmo estiver em pleno funcionamento, o que facilita uma maior disponibilidade, já que o equipamento vai sofrer intervenção, apenas no limiar estabelecido antecipadamente pelo departamento de manutenção. Entende-se com isso, que a manutenção preditiva antecipa a falha do equipamento e quando se decide realizar a intervenção para o conserto, ocorre na verdade uma manutenção corretiva programada. As condições básicas para que seja estabelecido este tipo de manutenção, são as seguintes: o equipamento, sistema ou instalação deve permitir algum tipo de monitoramento. O equipamento, sistema ou instalação deve ter a escolha por este tipo de manutenção justificada pelos custos envolvidos. As falhas devem ser originadas de causas que possam ser monitoradas e ter sua progressão acompanhada. (NOGUEIRA, GUIMARÃES, SILVA, 2012) Ou seja, podemos dizer que a manutenção preditiva, é empenho realizado para acompanhar e monitorar as condições apresentadas pelo equipamento. A mesma está condicionada a detecção precoce dos sintomas da falha. O que demanda ter instrumentos de medição adequados, bom programa de computador e treinamento de pessoal é que faz com que a manutenção preditiva seja uma das mais baratas e seguras para conduzir uma política de manutenção.
2.3.4 Manutenção Detectiva
A manutenção detectiva é a atuação efetuada em sistemas de proteção, buscando detectar falhas ocultas ou não perceptíveis ao pessoal de operação e manutenção (PINTO 2001, pg. 44). A identificação de falhas ocultas é primordial para gerar confiabilidade. Em sistemas complexos essas ações devem ser efetuadas por pessoal da área de manutenção, com treinamento e habilitação para tal, assessorado pelos operadores das máquinas. Atualmente torna se necessário o uso de máquinas com controle autônomo e a crescente a utilização de computadores para o controle de processo nos mais diversos tipos de plantas fabris (PINTO 2001, pg. 44). A manutenção detectiva começou a ser mencionada na literatura a partir da década de 90. Sua denominação Detectiva está ligada à palavra Detectar, traduzida do inglês traduz Detective Maintenance. (KARDEC; NASCIF, 2002). Desse modo, Kardec e Nascif (2002), definem a manutenção detectiva como a atuação efetuada em sistemas de proteção, buscando detectar falhas ocultas ou não perceptíveis ao pessoal de operação e manutenção. Conforme Kardec e Nascif (2002), a identificação de falhas ocultas é primordial para garantir a confiabilidade. Em sistemas complexos essas ações só devem ser levadas a efeito por pessoal da área de manutenção, com treinamento e habilitação para tal, assessorado pelo pessoal da operação. Atualmente, é crescente a utilização de computadores para instrumentação e controle de processo nos mais diversos tipos de plantas industriais.
2.3.5 Engenharia de Manutenção
Praticar a Engenharia de Manutenção significa uma mudança cultural na empresa, ou seja, é deixar de ficar consertando continuamente, para procurar as causas básicas, modificar situações permanentes de mau desempenho, deixar de conviver com problemas crônicos, melhorar padrões e sistemáticas, desenvolver a manutenibilidade, dar feedback ao projeto, interferir tecnicamente nas compras (PINTO 2001, pg. 46).
2.4 MANUTENÇÃO ESTRATÉGICA
A manutenção, para ser estratégica, precisa estar voltada para os resultados empresariais da organização. É preciso, sobretudo, deixar de ser apenas eficiente para se tornar eficaz, ou seja, não basta apenas reparar o equipamento ou instalação tão rápido quanto possível, mas é preciso, principalmente, manter função do equipamento disponível para a operação reduzindo a probabilidade de uma parada de produção não planejada (PINTO, 2001, pg.11).
2.4.1 Terceirização
Segundo Pinto (2001. Pg.194) a terceirização é a “transferência para terceiros de atividades que agregam competitividade empresarial, baseada numa relação de parceria. ” A terceirização tem uma relação de parceiras, ou seja, sobretudo que seja, uma relação de resultados empresariais para as partes envolvidas, trazendo vantagens competitiva para a empresa contratante, através de uma economia de escala e para a empresa contratada através de uma maior especialização, comprometimento com resultados e autonomia gerencial (PINTO, 2001, pg.194).
Praticar a Engenharia de Manutenção significa uma mudança cultural na empresa, ou seja, é deixar de ficar consertando continuamente, para procurar as causas básicas, modificar situações permanentes de mau desempenho, deixar de conviver com problemas crônicos, melhorar padrões e sistemáticas, desenvolver a manutenibilidade, dar feedback ao projeto, interferir tecnicamente nas compras (PINTO 2001, pg. 46).
2.4 MANUTENÇÃO ESTRATÉGICA
A manutenção, para ser estratégica, precisa estar voltada para os resultados empresariais da organização. É preciso, sobretudo, deixar de ser apenas eficiente para se tornar eficaz, ou seja, não basta apenas reparar o equipamento ou instalação tão rápido quanto possível, mas é preciso, principalmente, manter função do equipamento disponível para a operação reduzindo a probabilidade de uma parada de produção não planejada (PINTO, 2001, pg.11).
2.4.1 Terceirização
Segundo Pinto (2001. Pg.194) a terceirização é a “transferência para terceiros de atividades que agregam competitividade empresarial, baseada numa relação de parceria. ” A terceirização tem uma relação de parceiras, ou seja, sobretudo que seja, uma relação de resultados empresariais para as partes envolvidas, trazendo vantagens competitiva para a empresa contratante, através de uma economia de escala e para a empresa contratada através de uma maior especialização, comprometimento com resultados e autonomia gerencial (PINTO, 2001, pg.194).
A terceirização da manutenção é boa para as empresas pois, com esse serviço aumenta a qualidade, reduz os custos, aumenta a especialização dos que prestam esse serviço, porém, também pode trazer algumas desvantagens quando se terceiriza sem uma adequada visão estratégica, como por exemplo, a empresa se torna dependente de terceiros, também pode aumentar o risco de perder em qualidade, aumentos dos custos quando simplesmente se empreiteiriza (PINTO, 2001, pg.198).
2.4.2 Meta-estratégias
Na gestão da manutenção são observados três cenários meta-estratégicos primitivos, são eles:
2.4.2.1 Manutenção Centrada no Equipamento As decisões de manutenção centradas no equipamento, são tomadas tendo em mente o que é bom para a máquina. As necessidades dos equipamentos são atendidas, mesmo com risco para a missão. O processo cede espaço para a manutenção (Sellitto). A manutenção centrada no equipamento ocorre, quando a perda da quebra é superior ao valor do processo e não vale a pena assumir o risco como por exemplo em, ônibus e aeronaves (Sellitto).
2.4.2.2 Manutenção Centrada no Processo As decisões de manutenção centradas no processo, são tomadas tendo em mente o que é bom para o processo. As necessidades da missão são atendidas, mesmo com risco para os equipamentos. A manutenção aproveita as oportunidades cedidas pelo processo (Sellitto). Esse tipo de manutenção ocorre quando a perda por quebra é inferior ao valor do processo e vale a pena assumir o risco, como por exemplo em máquinas operatrizes (Sellitto).
2.4.2.3 Meta-modelos de Manutenção As decisões de manutenção são tomadas tendo em mente modelos já propostos por especialistas. As ações são baseadas em prescrições de boas práticas formuladas por especialistas e fabricantes. A manutenção adota um programa geral já testado em outras situações (Sellitto).
2.4.3 Estratégias Mistas
Estratégias mistas é analisar a situação da empresa por meio de um diagnóstico estratégico relacionado a aspectos como qualidade, equipamento, serviços e processos valor (Sellitto). Na figura 1 a seguir temos ilustrado o modelo da tabela de Estratégias Mistas.
Figure 1 - Modelo Estratégias Mistas
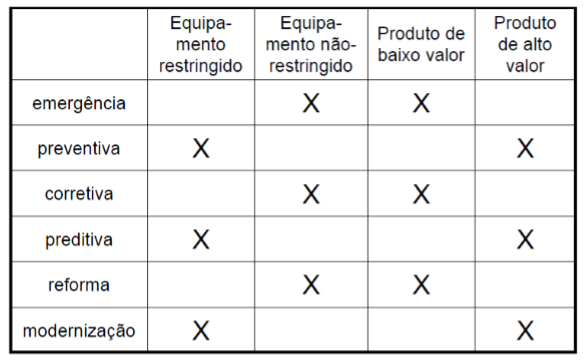
Fonte: Sellitto, Miguel
De acordo com SELLITTO, as estratégias mistas são utilizadas para saber quando e como fazer uma manutenção dependendo do tipo e valor do equipamento.
2.4.4 Cenários Estratégicos Mistos
Quando for aplicada à manutenção, a gestão estratégica buscará garantir a maior disponibilidade possível dos equipamentos e consumir o mínimo possível de recursos (Sellitto). Para isso é utilizado algumas tabelas como pode ser observado na figura 2 o modelo de tabela.
Figure 2 - Modelo Cenários Estratégicos Mistos
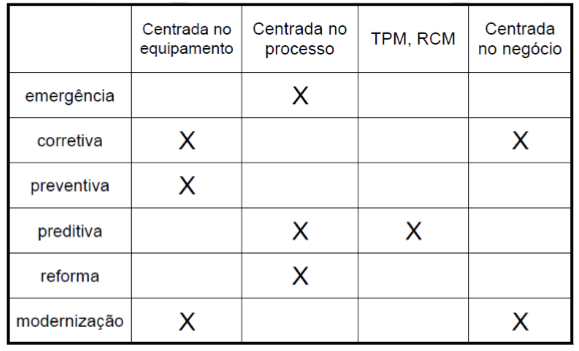
Fonte: Sellitto, Miguel
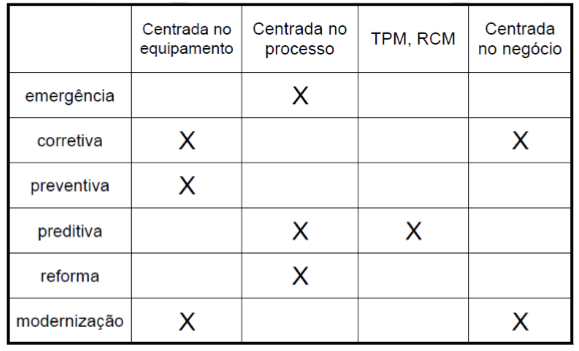
Fonte: Sellitto, Miguel
Com esta tabela é possível analisar o tipo de manutenção a ser utilizada, de acordo com a meta-estratégica, ou seja, se ele é centrado no processo, no equipamento ou no negócio (Sellitto).
2.4.5 Matriz Estratégica
A matriz estratégica é feita de acordo com o equipamento, indicando o que é já é feito e o que deve ser melhorado. O modelo da matriz pode ser observado na figura 3.
Figure 3 - Modelo Matriz Estratégica
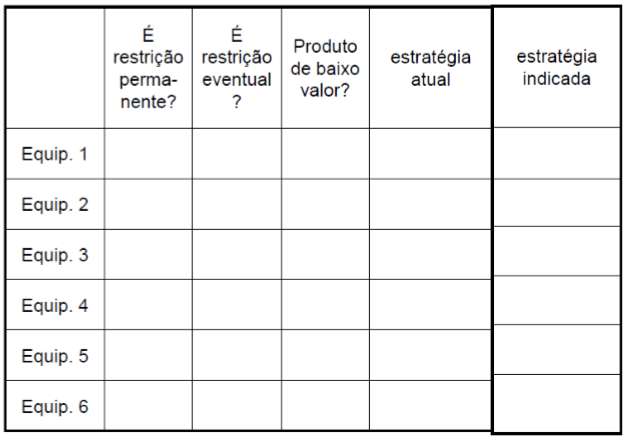
Fonte: Sellitto, Miguel
A gestão estratégica da manutenção é a única responsável por definir onde, quando e porque aplicar cada tipo de manutenção (Sellitto).
2.4.6 Estratégia da Produção
Conforme SELLITTO, a estratégia de produção persegue os seguintes objetivos: Redução de custo; Aumento de qualidade; Aumento na confiabilidade no prazo de entrega: preventiva; Aumento de flexibilidade; e Promoção da inovação. Ainda de acordo com SELLITTO, para cada objetivo de produção, é mais adequada uma estratégia de manutenção: Redução de custo: emergência; Aumento de qualidade: preditiva; Aumento na confiabilidade no prazo de entrega: preventiva; Aumento de flexibilidade: corretiva; e Promoção da inovação: modernização.
2.5 SISTEMAS DE INFORMAÇÃO
De acordo com Pinto (2001, pg. 79) nos dias de hoje é possível encontrar no mercado uma ampla gama de softwares que atendem desde a manutenção de uma pequena empresa, que possua um quadro de 20 funcionários, até sistemas bastante sofisticados para as maiores empresas. A tendência é que todas as empresas estejam interligadas, e assim os dados podem ser acessados facilmente por qualquer pessoa e em qualquer área. Os sistemas de informação ajudam a planejar o serviço, com a programação dos serviços, controla e execução do serviço, administra os estoques, entre outros tantos ganhos que a empresa pode ter com a utilização de um sistema de informação para a manutenção (PINTO, 2001, pg. 84).
2.4.6 Estratégia da Produção
Conforme SELLITTO, a estratégia de produção persegue os seguintes objetivos: Redução de custo; Aumento de qualidade; Aumento na confiabilidade no prazo de entrega: preventiva; Aumento de flexibilidade; e Promoção da inovação. Ainda de acordo com SELLITTO, para cada objetivo de produção, é mais adequada uma estratégia de manutenção: Redução de custo: emergência; Aumento de qualidade: preditiva; Aumento na confiabilidade no prazo de entrega: preventiva; Aumento de flexibilidade: corretiva; e Promoção da inovação: modernização.
2.5 SISTEMAS DE INFORMAÇÃO
De acordo com Pinto (2001, pg. 79) nos dias de hoje é possível encontrar no mercado uma ampla gama de softwares que atendem desde a manutenção de uma pequena empresa, que possua um quadro de 20 funcionários, até sistemas bastante sofisticados para as maiores empresas. A tendência é que todas as empresas estejam interligadas, e assim os dados podem ser acessados facilmente por qualquer pessoa e em qualquer área. Os sistemas de informação ajudam a planejar o serviço, com a programação dos serviços, controla e execução do serviço, administra os estoques, entre outros tantos ganhos que a empresa pode ter com a utilização de um sistema de informação para a manutenção (PINTO, 2001, pg. 84).
3 METODOLOGIA
Segundo os autores Lakatos e Marconi (2006, p.83) o método científico “é o conjunto de atividades sistemáticas e racionais que, com maior segurança e economia, permite alcançar o objetivo – conhecimentos válidos e verdadeiros –, traçando o caminho a ser seguido, detectando erros e auxiliando as decisões dos cientistas”. A metodologia de pesquisa aplicada neste trabalho ocorreu através de um estudo de caso, de cunho exploratório, qualitativo, descritivo, documental, bibliográfico e observação, com propósito de identificar e analisar os principais processos de manutenção de equipamentos industriais. Este estudo foi realizado em uma indústria fabricante de móveis localizada no noroeste do estado do Rio Grande do Sul. A metodologia utilizada partiu da revisão bibliográfica sobre o assunto com vistas a conhecer a literatura disponível sobre manutenção de equipamentos industriais e subsidiar as referências iniciais do estudo estabelecendo conceitos a serem pesquisados. A partir disto, foram realizadas visitas de estudo na indústria abordando a maneira pela qual a mesma realiza a manutenção de seus equipamentos desenvolvendo um planejamento de uma nova estratégia de manutenção baseado na prevenção. Portanto este estudo seguiu basicamente três partes metodológicas, onde no primeiro momento apresentaremos a indústria e seus equipamentos utilizados no processo de produção, informando suas características mais relevantes. No tópico seguinte, foi determinado se a indústria dispõe e vem realizando um processo manutenção de equipamentos e como e quando realiza esse processo. No último tópico, realizaram-se a análise das informações coletadas comparadas com base no referencial bibliográfico e observações propondo um plano de manutenção industrial no setor moveleiro.
3.1 APRESENTAÇÃO DA EMPRESA
A empresa surgiu em 1989 produzindo estofados para salas de estar. Trabalhavam em um local com uma estrutura de 60m² e tinham apenas duas pessoas. Já em 1991 eles alugaram um prédio de 600m² e contavam com uma equipe de 30 pessoas, passando a atender o mercado estadual. Em 1992 foi inserido na linha de produtos, mesas e cadeiras em madeira. Em 1993 foi se instalar em uma área própria de 960m², na área industrial de Três de Maio. A expansão do mercado possibilitou que a Móveis Canção firmasse parcerias com grandes redes varejistas do Estado, tornando-se necessários investimentos em tecnologias para produção em maior escala. Em 1994 a empresa começou a exportar os produtos para países como Argentina, Uruguai, Chile, Canadá, África, Guatemala e Estados Unidos. No ano seguinte a Móveis Canção deixou de produzir a linha de estofados e focaram na produção de mesas e cadeiras. A instalação foi ampliada para 2.500m², foi investido em equipamentos e conseguimos com a contribuição de uma equipe competente, atender a demanda do mercado nacional e internacional. Em 1997 o número de funcionários chegou a cem. Nesse ano foi instalado uma unidade de usinagem da madeira em um pavilhão de 3 mil m², em um terreno próprio, com 45 mil m² no Mato Grosso, na cidade de Tapurah.
No ano 2000 a fábrica de Três de Maio já empregava 200 pessoas em consequência da demanda do mercado e do reconhecimento da qualidade dos produtos. A empresa passou a ser ainda mais reconhecidos no mercado internacional, nos tornando uma das principais fábricas de mesa e cadeiras do Brasil. Neste mesmo ano, foi firmado parcerias importantes com lojistas, distribuidores e redes varejistas da Argentina. Desta tornaram-se líderes de vendas no segmento de copas do país vizinho. Em 2004 a Móveis Canção incorpora a Móveis Deiss, de Mondaí, Santa Catarina, que até então, era o principal concorrente da Móveis Canção no segmento de copas. Com essa aquisição, criamos a filial dois, que continuou por aproximadamente dois anos, produzindo na planta fabril da Móveis Deiss. No ano de 2006 inaugurou a nova planta fabril da filial dois, em Mondaí, Santa Catarina. A unidade foi planejada para produzir os produtos com a qualidade já conhecida no mercado. O espaço da fábrica é de 3 mil m² e a equipe formada por 80 pessoas. Também foi deferido o registro da marca Móveis Canção® pelo INPI (Instituto Nacional de Propriedade Individual). Em 2007 foram realizadas ações voltadas à preservação do meio ambiente. A partir desse ano a Móveis Canção começou a atuar com uma maior consciência ecológica, plantando mudas de árvores onde já alcançou a marca de 120 mil árvores plantadas. Em 2008 ela incorpora a Tok & Arte Indústria de Móveis Ltda. e a marca dbLARE, agregando ao mix de produtos, as linhas de cozinhas moduladas e planejadas. No dia 8 de agosto de 2009, foi comemorado 20 anos de Móveis Canção, contando nas três unidades com um total de 220 colaboradores e 19.000m2 de área construída. Nossos planos para o futuro são muitos, mas os principais são continuar conquistando o mercado, gerar desenvolvimento e produzir com qualidade.
3.2 DELIMITAÇÃO DO PROCESSO DE MANUTENÇÃO EXISTENTE
O modelo de manutenção existente na empresa é a Manutenção Corretiva
não
Planejada, conhecida popularmente como “quebra conserta”. A manutenção é terceirizada, visto que a empresa não mantém profissionais internos que trabalhem exclusivamente na manutenção. Os gastos com a manutenção das máquinas fecharam neste semestre em R$ 11.594,65 de despesa por mês, nesta despesa está incluso peças, frete, mão-deobra do técnico que se deslocou para fazer a manutenção e diárias. Já com o mecânico terceirizado a empresa gasta por mês R$ 3.550.00. Com base nestes valores, mostra-se necessário aplicar uma melhoria no plano de gestão da manutenção, através de uma nova abordagem.
4 APRESENTAÇÃO E ANÁLISES DOS RESULTADOS
O processo manutenção foi delimitado para atender as necessidades latentes do processo produtivo, visando evitar que os gargalos da produção (máquinas que limitam a capacidade produtiva da empresa) convertam se em hora/máquina parada. Através do presente artigo foi criado um modelo de gestão da manutenção, que pode e deve ser utilizado pelos responsáveis da manutenção da empresa estudada, aumentado a produtividade e a confiabilidade da empresa. Criou-se planilhas de controle para a manutenção, que serviram de base para o histórico de cada máquina, tendo assim um respaldo para o sistema de gestão da manutenção a ser instalada. Optou-se por uma abordagem inicial baseada na manutenção preventiva, a qual terá uma vida modesta, sendo depois substituída por uma manutenção preditiva. Considerando que a empresa em questão não possuía um controle de manutenção da sua produção, e nem mesmo um acompanhamento contínuo, foi implementado um checklist para cada máquina, para se realizar um acompanhamento e identificação de possíveis problemas que podem acontecer no dia-a-dia. Desta forma é possível identificar toda vez que a máquina apresentar uma variabilidade, facilitando assim a tomada de decisão, e manter a qualidade e padrões apropriados dos produtos. Foi feita a análise e plano de manutenção de seis máquinas diferentes: Fresadora, Coladeira, Furadeira, Respigadeira, Envernizadora, Lixadeira, Transfer e Túnel.
4.1 PROPOSTA DE PLANO DE MANUTENÇÃO DAS MÁQUINAS
4.1.1 Fresadora
Fresadora é uma máquina de movimento continuo da ferramenta, destinada a usinagem de materiais. Remove-se cavacos por meio de uma ferramenta de corte chamada fresa. A operação de fresagem consta da combinação de movimentos simultâneos da ferramenta e da peça a ser usinada simultaneamente. O centro de furação da empresa em estudo, que possui uma fresadora cujo o modelo é CYFLEX F 900 e marca SCM, analisando seu manual foi possível realizar um checklist a ser seguido, como na figura 4.
Figure 4 - Checklist Fresa
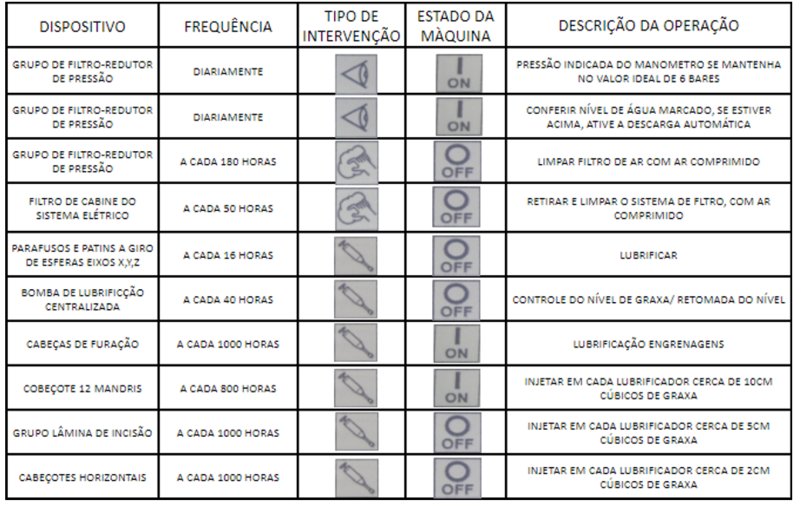
Fonte: Autores
4.1.2 Coladeira
Um dos itens que pode gerar muito valor agregado é a colagem da borda dos móveis e esta é a função da máquina coladeira. O checklist realizado para a coladeira, modelo AH/005921 e marca STEFANI, pode se ver na figura 5
Figure 5 - Checklist Coladeira
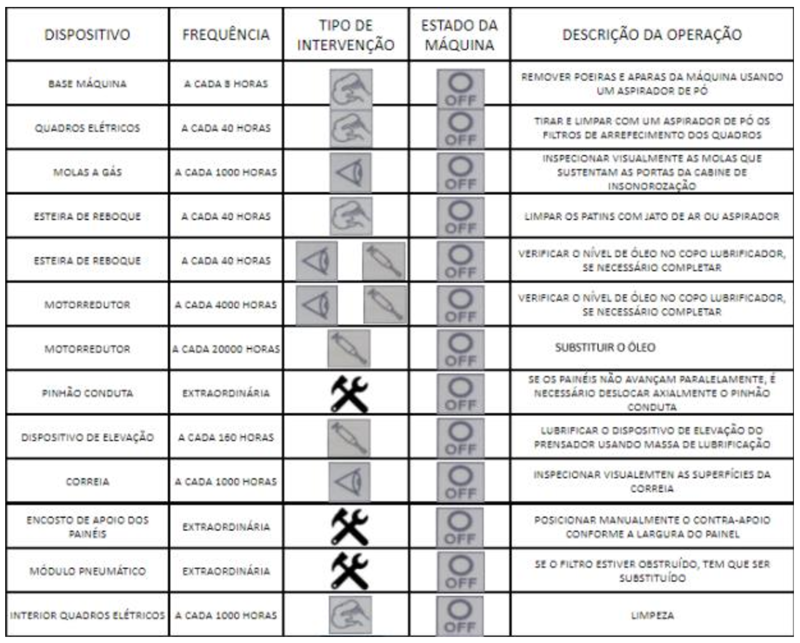
Fonte: Autores
4.1.3 Furadeira
Em sequência do processo de análise encontra-se a furadeira, a qual é uma máquina que tem como função principal executar furos nos mais diversos tipos de materiais. A furadeira da empresa em estudo é a furadeira com bipartido, modelo F500B, marca LIDEAR, como na figura 6
Figure 6 - Checklist Furadeira
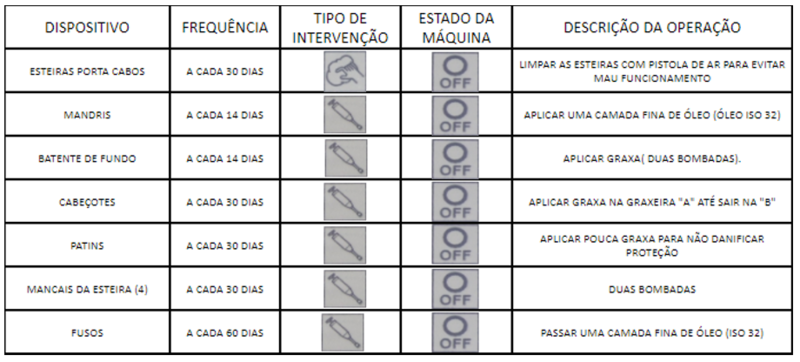
Fonte: Autores
4.1.4 Respigadeira
Outra máquina foi a respigadeira automática, modelo RA-2M, marca HARWAR cujo o checklist pode ser visto na imagem 7 abaixo.
Figure 7 - Checklist Respigadeira
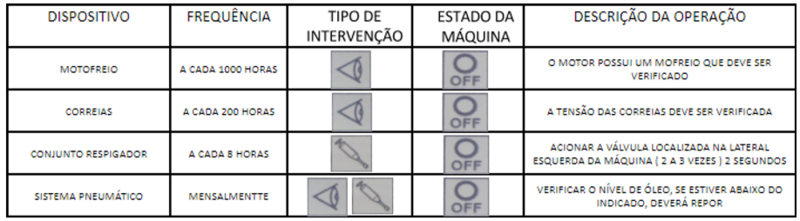
Fonte: Autores
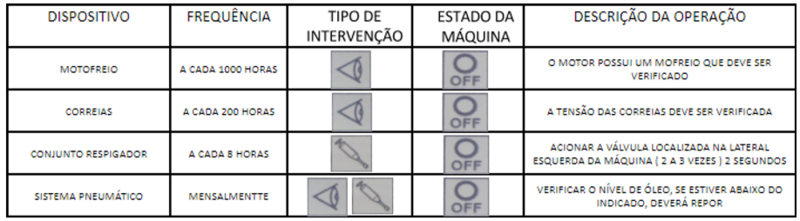
Fonte: Autores
A respigadeira, tem como função moldar os encaixes das pernas e suportes das cadeiras.
4.1.5 Envernizadora
Na sequência foi realizado o checklist da envernizadora/tingidora modelo ETR/3 e CM ETRDR, marca CRIPPA, o qual pode ser visto na figura 8 abaixo. A Envernizadora é uma máquina que oferece tanto a solução para aplicação de Verniz de Cura Ultravioleta (UV) como a de Cura Infravermelho (IR), que é adequada para se obter uma ancoragem perfeita do verniz sobre toner, offset ou impressões digitais.
4.1.5 Envernizadora
Na sequência foi realizado o checklist da envernizadora/tingidora modelo ETR/3 e CM ETRDR, marca CRIPPA, o qual pode ser visto na figura 8 abaixo. A Envernizadora é uma máquina que oferece tanto a solução para aplicação de Verniz de Cura Ultravioleta (UV) como a de Cura Infravermelho (IR), que é adequada para se obter uma ancoragem perfeita do verniz sobre toner, offset ou impressões digitais.
Figure 8 - Checklist Envernizadora
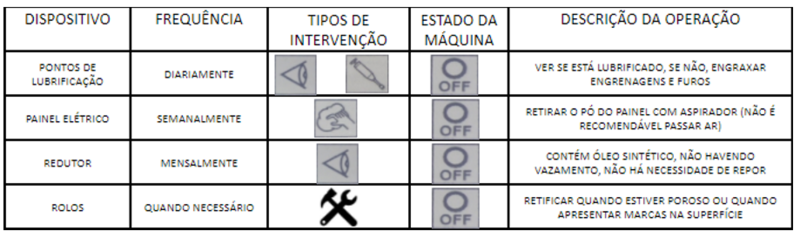
Fonte: Autores
4.1.6 Lixadeira
Para a sequência da linha de produção foi realizado o checklist da máquina lixadeira, o qual pode ser visto na figura 9 abaixo. A lixadeira é uma máquina que lixa o material com o objetivo de torná-lo apto a receber a tintura, envernizamento ou estampagem.
Figure 9 - Checklist Lixadeira
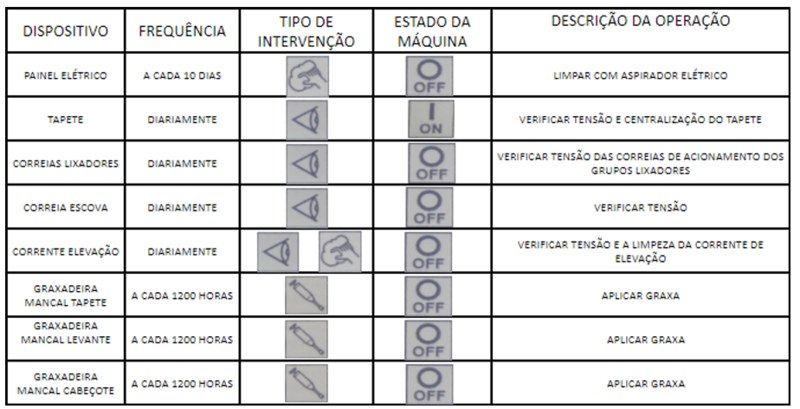
Fonte: Autores
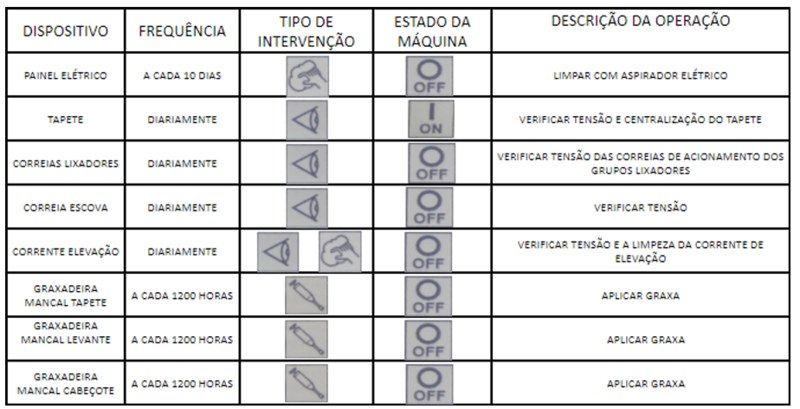
Fonte: Autores
4.1.7 Transfer
Outra máquina que foi realizado o checklist foi o tranfer, o qual o modelo é MP 83 TF e a marca é MASTER PAINT, o qual pode ser visto na figura 10 abaixo. O Transfer são os roletes que transferem uma peça de uma máquina até a outra.
Figure 10 - Checklist Transfer
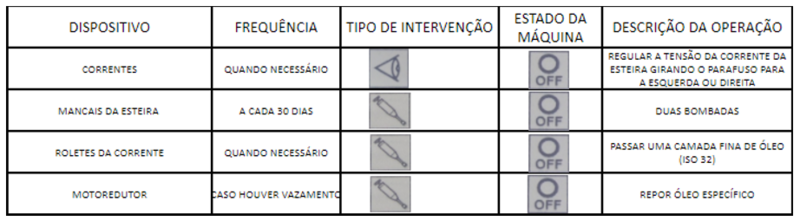
Fonte: Autores
4.1.8 Túnel
Para terminar a nossa linha de produção foi realizado o checklist da última máquina que é o túnel de secagem ultravioleta, modelo CMUV-I/UV-II e marca CRIPPA, pode ser visto na figura 11 abaixo. O Túnel é uma máquina que realiza a secagem ultravioleta do produto que foi aplicado.
Figure 11 - Checklist Túnel de Secagem
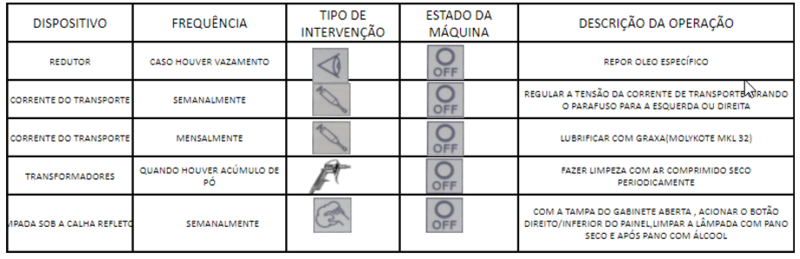
Fonte: Autores
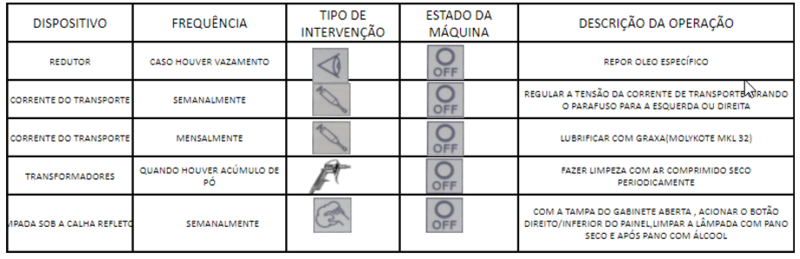
Fonte: Autores
4.2 CONTROLE DA MANUTENÇÃO DAS MÁQUINAS
Para que seja possível utilizar o checklist, anotando as datas de manutenção, adicionou-se algumas colunas em cada checklist, conforme figura 12.
Figure 12 - Checklist mensal
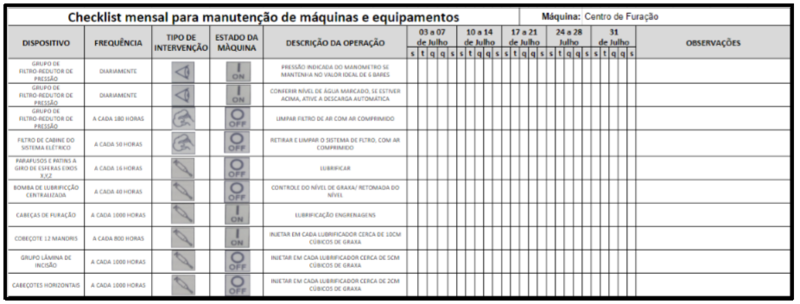
Fonte: Autores
Desta forma, é preciso imprimir mensalmente a folha de checklist de cada máquina e, conforme for feita a manutenção da máquina, o operador marca com um “X” na data em que foi feita.
4.3 CONTROLE FINANCEIRO DA MANUTENÇÃO
A realização da manutenção corretiva se mantém terceirizada, considerando o alto custo de manter um profissional qualificado para a empresa, porém, para realizar o controle desta manutenção, criou-se uma planilha de controle de todas as manutenções realizadas na empresa, contendo a máquina, modelo, data, valor e motivo da manutenção, como pode ser visto na figura abaixo.
4.3 CONTROLE FINANCEIRO DA MANUTENÇÃO
A realização da manutenção corretiva se mantém terceirizada, considerando o alto custo de manter um profissional qualificado para a empresa, porém, para realizar o controle desta manutenção, criou-se uma planilha de controle de todas as manutenções realizadas na empresa, contendo a máquina, modelo, data, valor e motivo da manutenção, como pode ser visto na figura abaixo.
Figure 13 - Controle Financeiro de Manutenção
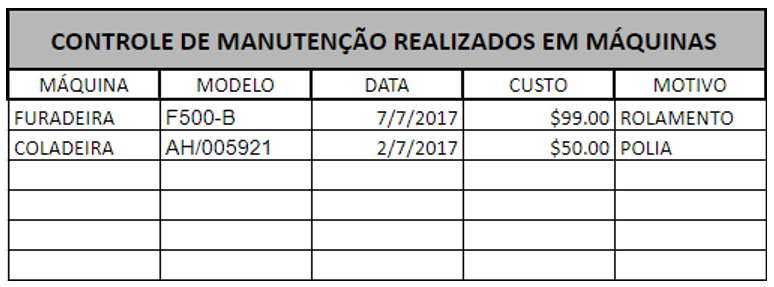
Fonte: Autores
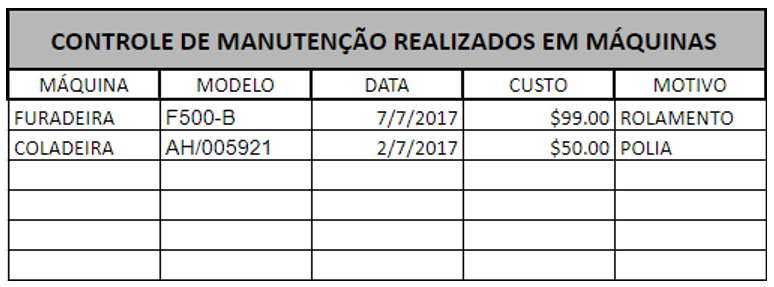
Fonte: Autores
Com esta planilha se tem um controle total de todos os gastos com manutenç&ati